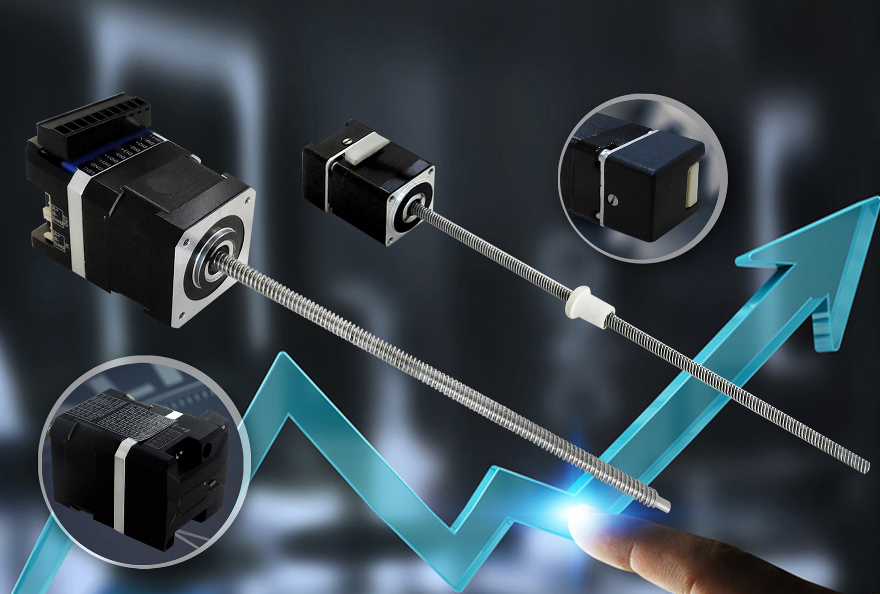
Linear stepper motors are a new type of motor known for their high efficiency, precision, and low noise, making them increasingly popular in industrial applications.
Performance Advantages
Linear stepper motors have several distinct performance advantages. They are highly efficient, precise, and quiet, which has led to their widespread adoption in various industrial fields, such as automated production lines and robotics. Their high efficiency and precision allow for accurate control of the motor’s speed and position, making them ideal for applications requiring precise movement. Additionally, their low noise makes them suitable for use in precision machinery manufacturing, further meeting the demands of industrial applications.
Broader Applications
The development of linear stepper motors has expanded their range of applications, enhancing their role in industrial settings. These motors help achieve automated production, improve production efficiency, reduce costs, and enhance product quality, thereby boosting a company’s competitiveness in the market.
Future Opportunities
The advancement of linear stepper motors will bring new opportunities for industrial applications, providing more development prospects for businesses and greater benefits for society. In the future, linear stepper motors are expected to play an even more significant role, further driving the development of industries worldwide.
Mechanical Precision
Linear stepper motors are used for precise positioning. They operate by driving a mechanical output shaft in a step-by-step motion using a controllable motor. This allows for accurate displacement control, providing both positional and angular control in mechanical systems. These high-precision, low-noise, and low-vibration devices combine electronic and mechanical technology, making them increasingly prevalent in automation control systems, machine tool control systems, and various measurement devices.
Structure
A linear stepper motor comprises a motor, gearbox, reduction gears, bearings, and a slider. The motor is typically a standard brushless motor, while the gearbox is a cycloidal pinwheel reducer. The quality of the reduction gears and bearings determines the mechanical precision and durability. The slider supports the motor, and its sliding precision directly affects the positioning accuracy of the stepper motor.
Operating Principle
The principle of a linear stepper motor involves using a motor to drive the slider to achieve positioning. By controlling the motor's current, the displacement of the slider can be controlled, thus achieving precise positioning. The motor drives the slider, the slider pushes the output shaft, and the output shaft achieves positioning, enabling accurate displacement control.
Advantages
Linear stepper motors offer numerous advantages, including high precision, low noise, low vibration, high durability, easy installation, and simple maintenance. They can achieve precise displacement and angular control, making them vital in mechanical systems.
Applications
Linear stepper motors can be used in various measurement devices, machine tool control systems, and automation control systems. They are applicable in fields such as printing machines, rewinding machines, fabric inspection machines, plastic bending machines, welding machines, and woodworking machinery, enabling accurate positioning control.
Drawbacks
Despite their many advantages, linear stepper motors have some drawbacks. They are not suitable for high-speed operations, tend to have lower operational stability, and their control systems can be complex. Additionally, they may experience significant harmonic losses, and the efficiency of their brakes can be low.
Linear stepper motors are high-precision, low-noise, low-vibration devices with growing applications in automation control systems, machine tool control systems, and various measurement devices. They can achieve precise displacement and angular control, offering significant value in numerous industrial applications.